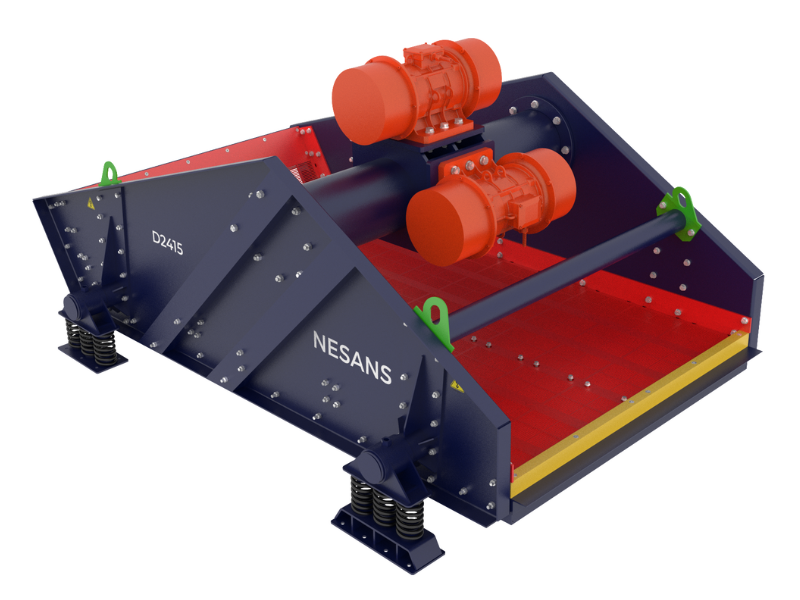
Dewatering Screen - D Series
The Nesans D Series Dewatering Screens are purpose-built for efficient moisture removal from washed sand, minerals, and other fine materials. Designed to deliver high drainage rates and minimal material loss, these screens are an essential component in any wet processing setup, ensuring clean, dry output suitable for storage or further processing.
With a compact footprint and high-frequency linear motion, the D Series delivers superior dewatering performance while maintaining structural integrity even under continuous heavy loads. Its rugged design, steep deck angle, and optimized screen media work together to maximize water removal and reduce cycle times.
Ideal for sand plants, mineral beneficiation, and industrial washing systems, the Nesans D Series offers consistent performance, low maintenance, and reliable operation, making it a trusted solution for achieving superior dewatering results.
Applications:
How It Works
The Nesans D Series Dewatering Screens operate using high-frequency linear vibration to efficiently separate water from fine materials. Material is fed onto a steeply inclined screen deck where rapid vibration causes the particles to form a compact bed. As the bed moves across the screen, water is effectively drained through the screening media, leaving behind a moisture-reduced product.
The screen is typically powered by two counter-rotating vibratory motors that create a linear motion, pushing the material forward while continuously removing surface water. This motion, combined with the deck slope and high G-force, ensures maximum dewatering efficiency with minimal material loss. The result is a cleaner, drier product ready for immediate handling or storage.
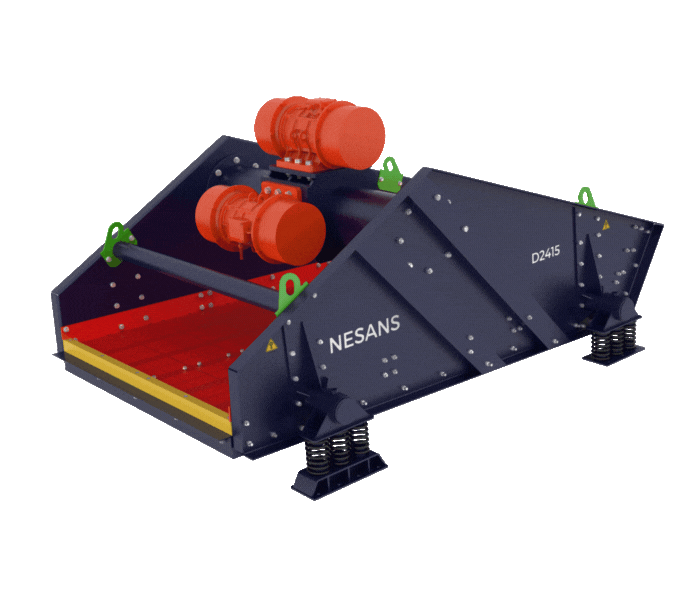
Features and Advantages
Specifications
Model No. | Max Length (mm) | Max Width (mm) | Max Feed Size (mm) | Dewatering Screen Power (kW) | Capacity (mtph) |
---|---|---|---|---|---|
D1206 | 1200 | 600 | -10 | 2 X 0.75 | 25 |
D1209 | 1200 | 900 | -10 | 2 X 0.75 | 30 |
D1809 | 1800 | 900 | -10 | 2 X 1.1 | 50 |
D1812 | 1800 | 1200 | -10 | 2 X 1.6 | 65 |
D2412 | 2400 | 1200 | -10 | 2 X 1.9 | 75 |
D2415 | 2400 | 1500 | -10 | 2 X 2.2 | 100 |
D3015 | 3000 | 1500 | -10 | 2 X 2.5 | 125 |
D3612 | 3600 | 1200 | -10 | 2 X 3.7 | 150 |
D3615 | 3600 | 1500 | -10 | 2 X 5 | 200 |
D4215 | 4200 | 1500 | -10 | 2 X 7.5 | 250 |
D4218 | 4200 | 1800 | -10 | 2 X 9.0 | 325 |
Model No. | Max Length (ft) | Max Width (ft) | Max Feed Size (in) | Dewatering Screen Power (hp) | Capacity (stph) |
---|---|---|---|---|---|
D1206 | 4 | 2 | -1/2 | 1 | 28 |
D1209 | 4 | 3 | -1/2 | 2 X 1 | 33 |
D1809 | 6 | 3 | -1/2 | 1.5 | 55 |
D1812 | 6 | 4 | -1/2 | 2 X 2 | 72 |
D2412 | 8 | 4 | -1/2 | 2 X 2.5 | 83 |
D2415 | 8 | 5 | -1/2 | 2 X 3 | 110 |
D3015 | 10 | 5 | -1/2 | 2 X 3.5 | 138 |
D3612 | 12 | 4 | -1/2 | 2 X 5 | 165 |
D3615 | 12 | 5 | -1/2 | 2 X 7.5 | 220 |
D4215 | 14 | 5 | -1/2 | 2 X 10 | 275 |
D4218 | 14 | 6 | -1/2 | 2 X 12 | 358 |
Product Gallery
Relevant Products
Contact Us
Want to Know More? Need a Quote? Please Complete the form below and our Sales Engineer will follow up shortly.