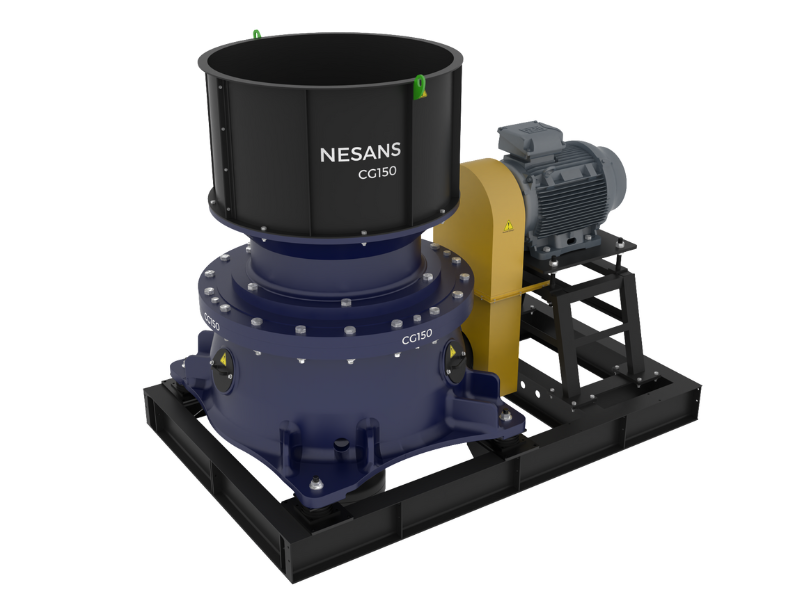
Cone Crushers - CG Series
The CG Series Cone Crusher is engineered for high-capacity performance and precise crushing across demanding applications. Its advanced chamber geometry and balanced design ensure consistent product shape and superior reduction. With optimized speed and stroke, it delivers efficient throughput while maintaining energy efficiency.
Built for versatility, the CG Series excels in secondary and tertiary crushing, handling a wide range of materials with ease. Whether in mining, quarrying, or aggregates production, it adapts seamlessly to site conditions. Its rugged build guarantees stable operation even under the toughest workloads.
Ease of maintenance, simplified access to critical components, and reduced downtime make the CG Series a reliable partner for continuous production. Heavy-duty parts ensure long equipment life and lower operating costs. This combination of performance, durability, and serviceability sets it apart in the crushing industry.
Applications:
How It Works
The CG Series Cone Crusher operates on the principle of compression crushing. Material is fed into the crushing chamber where it is compressed between a rotating mantle and a stationary concave liner. As the eccentric motion of the main shaft causes the mantle to gyrate, the material is progressively crushed to smaller sizes.
The crushed material moves downward through the narrowing chamber as it gets reduced in size, until it reaches the desired output dimension and exits through the bottom. This continuous process ensures uniform product gradation and high reduction efficiency. The precisely engineered chamber and control systems allow for consistent performance and minimal operational interruptions.
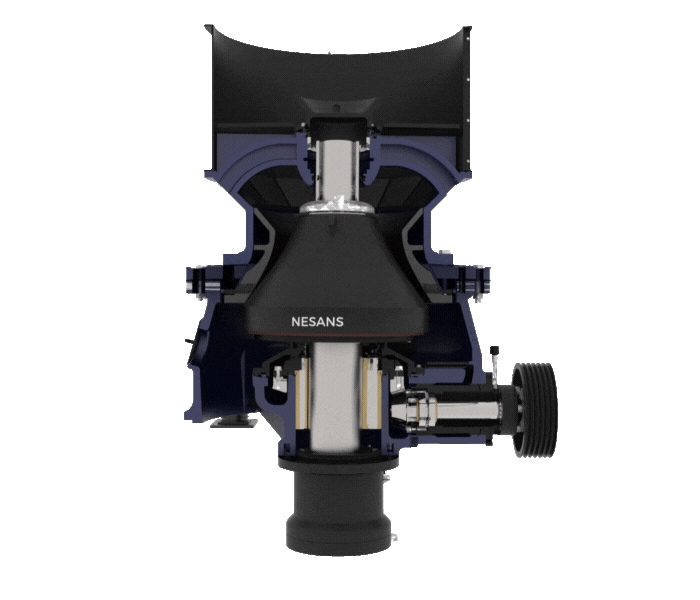
Features and Advantages
Specifications
Model No. | Feed Opening (mm) | Max Feed Size (mm) | CSS Range (mm) | Motor Power (Kw) | Crusher Weight (kg) | Capacity (mtph) |
---|---|---|---|---|---|---|
CG150 | 185 | 150 | 24-32 | 90-135 | 10200 | 90-200 |
CG150F | 90 | 50 | 12-28 | 90-135 | 10200 | 65-110 |
CG250 | 225 | 200 | 24-35 | 165-210 | 14100 | 150-310 |
CG250F | 85 | 60 | 14-35 | 165-210 | 14100 | 90-130 |
Model No. | Feed Opening (in) | Max Feed Size (in) | CSS Range (in) | Motor Power (Hp) | Crusher Weight (lb) | Capacity (stph) |
---|---|---|---|---|---|---|
CG150 | 7.5 | 6 | 0.9-1.3 | 120-180 | 22487 | 99-220 |
CG150F | 3 | 2 | 0.5-1.1 | 120-180 | 22487 | 72-121 |
CG250 | 9 | 8 | 0.9-1.4 | 220-280 | 31085 | 165-341 |
CG250F | 3.3 | 2.4 | 0.5-1.4 | 220-280 | 31085 | 99-143 |
Product Gallery
Relevant Products
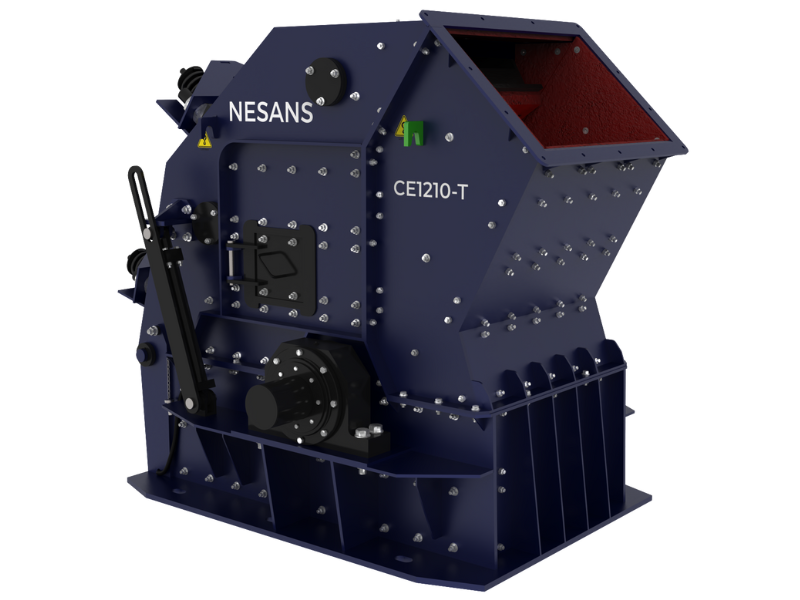
Horizontal Shaft Impact Crusher
Learn More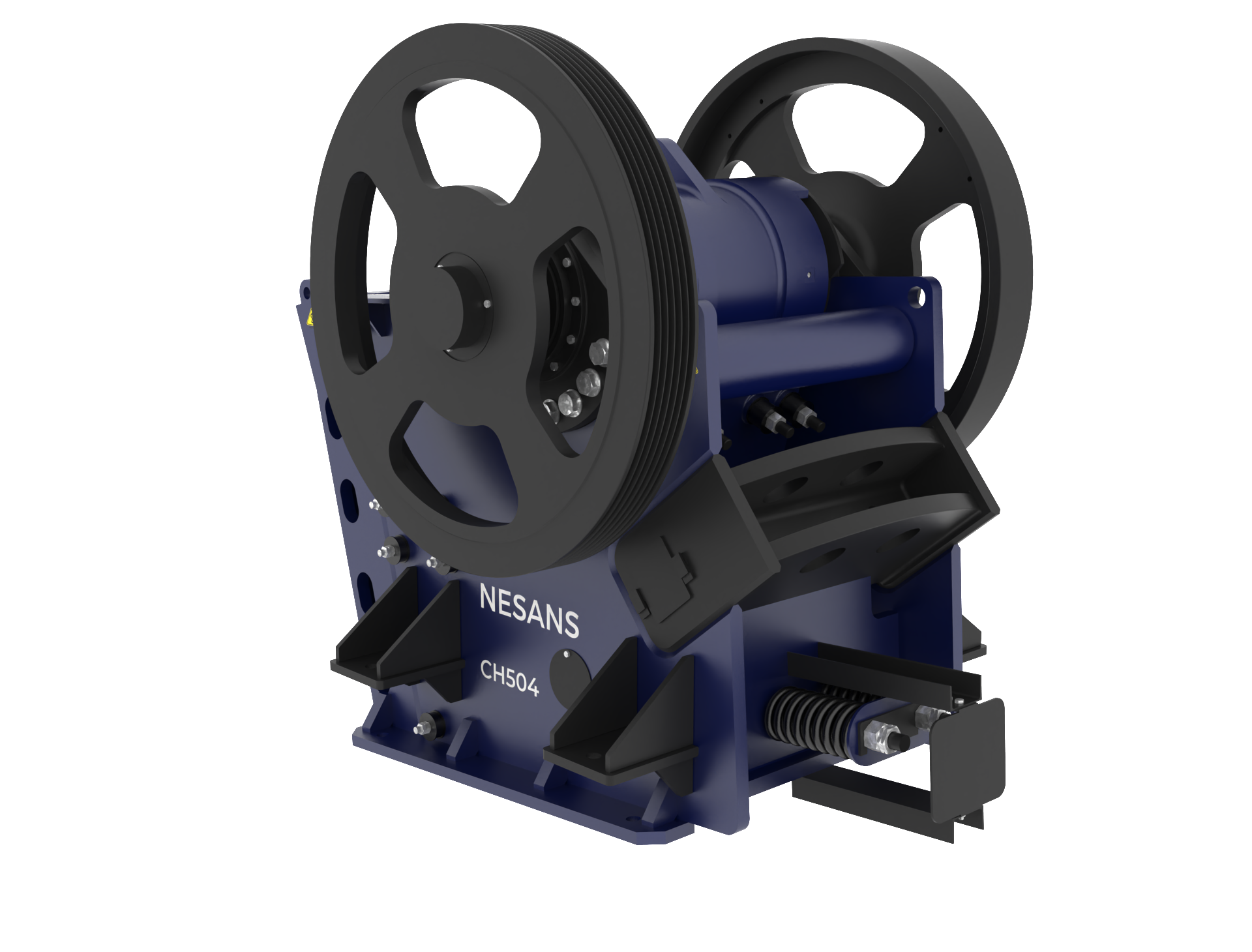
Jaw Crusher
Learn More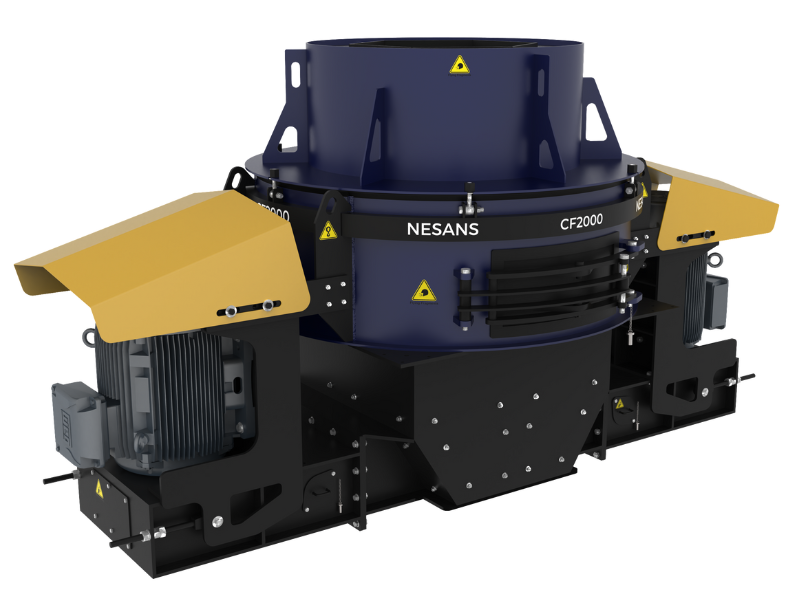
Vertical Shaft Impact Crusher
Learn MoreContact Us
Want to Know More? Need a Quote? Please Complete the form below and our Sales Engineer will follow up shortly.